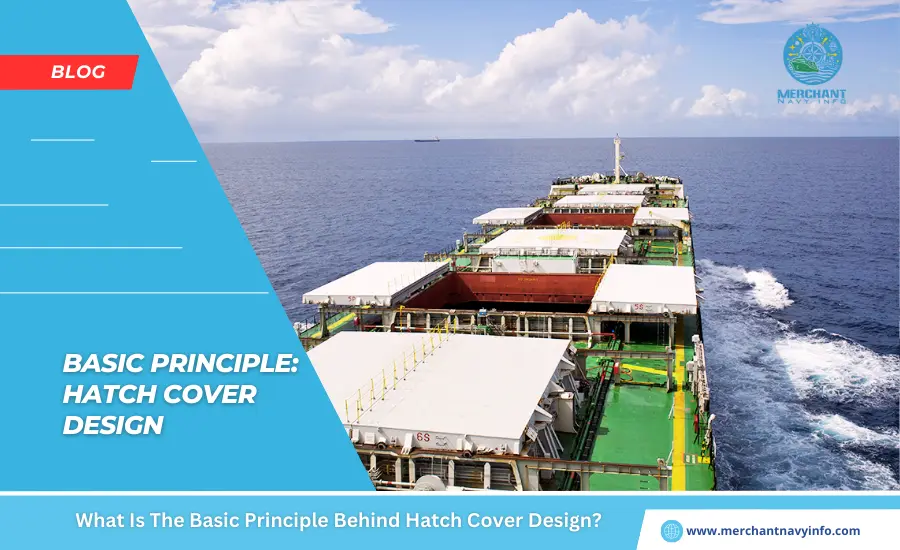
Hatch cover ships are designed to be efficient and also cost-effective both in initial investment and during operation while meeting the requirements of different types of cargo ships. The main purpose of ship hatch covers and coamings are to prevent water from ingressing into the holds and also protect the cargo from dampness and damage. Hatch covers also act as the barrier to the ship’s internal structure by withstanding exposure to green water in extreme weather conditions that can damage the ship’s internal structure through corrosion.
Types of Hatch Covers
The types of Hatch covers mostly used on board ships are:
- Lifting Type
- Rolling Type
- Folding Type
- Sliding Type
- Rolling Stow Type
Lifting-type hatch covers or lift-away hatch covers are generally used on container ships, while roller type (side roller, to be precise) is used on bulk carriers. Rolling types are divided into end rolling type, side rolling type, and also piggyback telescopic rolling type. Hinged Hatch Covers are typically used on cargo ships. However, these may sometimes vary depending on the storage space and type of cargo. Hinged Hatch Covers hinged hatch covers consist of two flat plates operated by a hydraulic arm. They can be installed on both weather decks and tween decks.
The main advantage of the hinged Hatch cover ship design is its size, which means fewer panels. Rolling Type Rolling hatch covers consist of two covers at the ends of the Hatch. Wheels are fitted to facilitate sliding the plates across the ship for sideways rotation and also longitudinally for end rotation. This type of Hatch cover ship is usually fitted on larger vessels. These are very heavy and very large and, therefore, require hydraulic cylinders to lift them into the rotating position.
Lifting Type Lift-Off Hatch Covers Can Be Classified Into Two Types:
- Single Panel Covers,
- Multi Panel Covers.
Single panel covers consist of one cover for each opening and are also mainly found on bulk carriers. Multi-panel covers allow one cargo space to be covered by several covers. They are most commonly found on longitudinally connected cellular container ships and also on transversely connected multipurpose cargo ships.
Stackable Cover Type
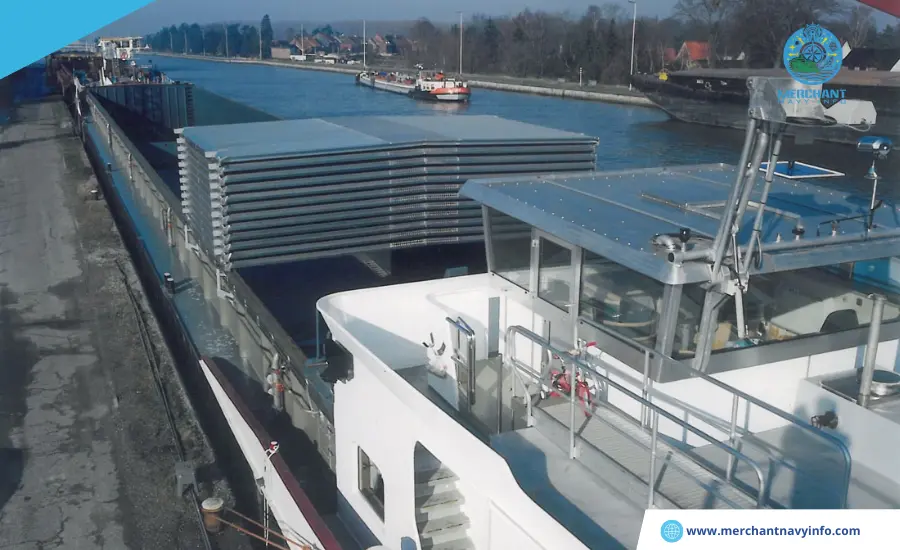
This type of equipment is used on ships with relatively small hatch covers. It consists of a hydraulically operated lifting crane system whose purpose is to lift the covers longitudinally and also stack them at one end or over an empty storage tank. It is relatively cheap and is mainly used on barges.
Hatch Cover Ship Design
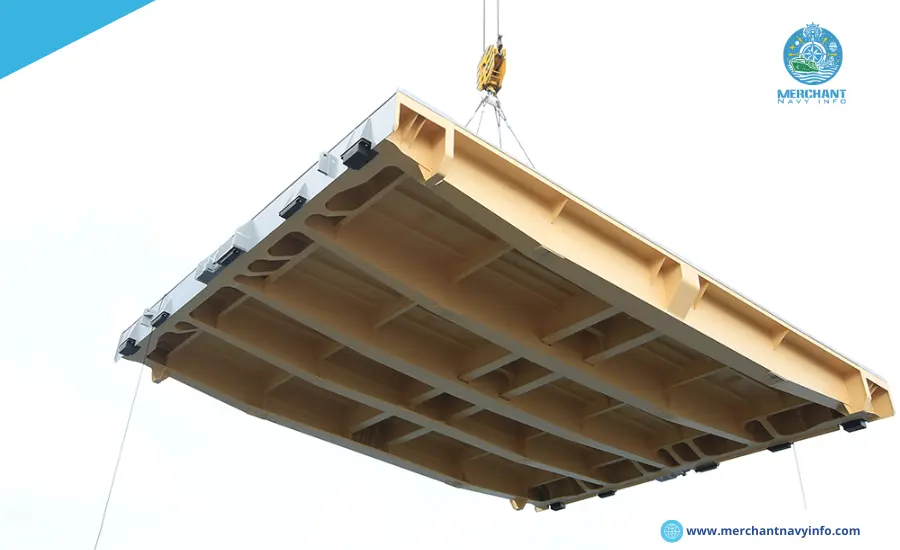
Designing a Hatch cover ship is not just about designing the cover and its coaming edges. Several important components ensure that the Hatch cover ship remains intact and effective for a long time. The important parts are:
- Bearing pads
- Fixing devices.
- Cleats and wedges
- Pontoons and panels
- Operating mechanisms
- Stoppers
- Drains and check valves
- Pushrods
To ensure the safety of cargo and the effectiveness of hatch covers and coamings, the above-mentioned components need to be maintained regularly.
Components Of Hatch Covers
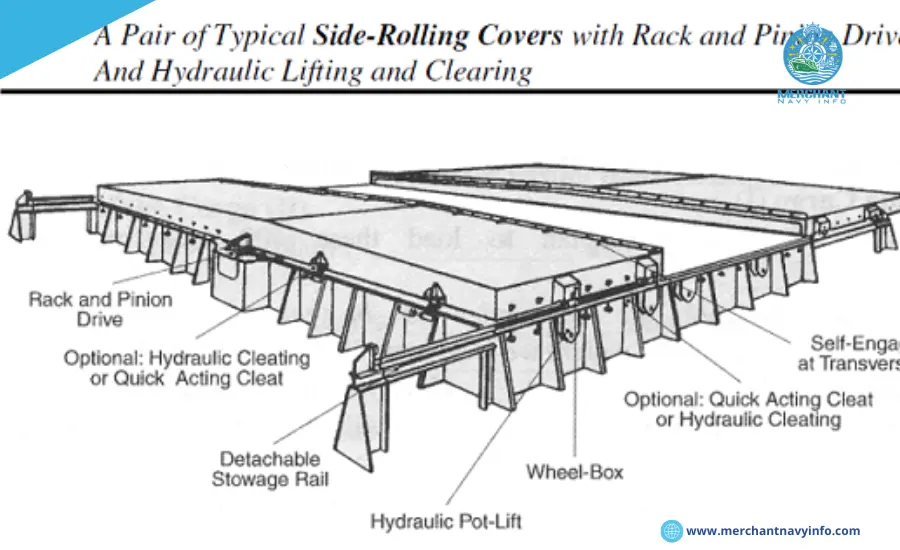
The general considerations while designing the various components of hatch covers are:
1. Deck opening:
The strength of the ship’s hull is determined by the size of the deck opening. Even for ships with hatch width more than 70% of the overall beam, high tensile steels should be used to ensure sufficient longitudinal strength. For ships with large hatches, detailed structural design and strength analysis should be carried out. Stress concentration points are usually at the corners of the openings and can be avoided by thick elliptical or parabolic plates.
2. Coaming Height:
Height is measured above the top of the deck. It is closed by a steel cover with a direct lock. However, coaming height can be omitted unless it poses a threat to the safety of the vessel. Most ships, especially bulk carriers, have a coaming height of about 1 to 1.8 m to accommodate more cargo. The coamings can also be designed to slope inwards to create a larger opening at deck level.
3. Design of Hatch Corners:
The designer must avoid an abrupt interruption in longitudinal strength at the ends of the side coamings. To ensure structural continuity, beams are extended beyond the ends of the Hatch to the appropriate end. Tapered brackets are usually used to extend the hatch coamings and reduce the stress concentrations. As mentioned earlier, the use of elliptical or parabolic plates at the corners also helps to reduce the stress concentrations, which lead to material fatigue and subsequent failure.
4. Drainage:
To avoid damage to delicate cargoes, adequate drainage facilities must be available. This can be achieved by providing a groove around the perimeter seal of the Hatch cover ship to ensure that water drains through holes in the coamings to the weather deck.
Container Ships Without Hatches
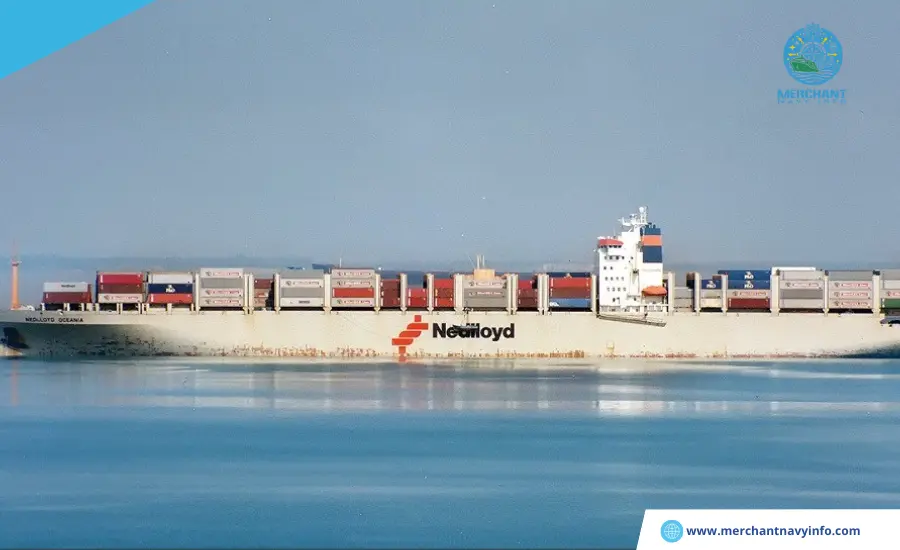
The concept of a container ship without hatches can be considered a revolutionary change in the field of cargo ship design. This is evident when looking at the disadvantages of container ships with hatch covers:
- The load-bearing capacity can be increased by reducing the weight of the heavy hatch covers.
- Since the hatch covers are mounted at a high position, their removal increases stability.
- It eliminates the time required for opening and closing the Hatch covers and, therefore, speeds up port operations.
- Individual vertical stacks can be removed without affecting other stacks. Previously, to access containers below deck, it was necessary to remove the containers from the hatch.
- It makes securing containers easier, whereas, in conventional container ships, containers had to be secured individually with lashing straps over the Hatch covers.
- It eliminates the need to maintain hatch covers, coamings, seals, cleats, etc. However, this concept also has various disadvantages.
- Firstly, the inflow of green water into the holds cannot be prevented, which may lead to damage to the internal structure.
- Secondly, the ship is exposed to torsion when empty, so these ships have relatively large torsion boxes.